by Steve Allen, VP Marketing and Innovation, ACL Staticide
Steve Allen's latest Guest Blog looks at the chemical replacements for AK-225 as it is approaches its total ban.
The EPA ban and elimination of HCFC-225 (also known as AK-225, and referred to that way from this point on) is a current topic of continuing concern in the area of electronics cleaning and printed circuit board (PCB) rework and repair. The banning of AK-225, effective January 1, 2015, will limit the number of available types of solvents for electronics cleaning. This will, once again, change the solvent cleaning landscape in our industry. It's important to understand what replacement chemistries will be available in 2015 and how this will affect end-users.
AK-225 falls under the EPA's Clean Air Act as a Class II ozone-depleting entity and is now defined as an Agency-Controlled Substance. It is thus deemed unlawful for any person to engage in interstate commerce of the solvent or any use of the substance unless it has been used, recovered, or recycled or used to produce another chemical, or finally, used as a refrigerant (until 1/1/2020). End-users may use, and continue to purchase, aerosols containing AK-225 made before January 1, 2015. Beginning January 1, 2015, AK-225 can only be used in the manufacture of end-user cleaning products if it has been used, recovered, and recycled, as per the Clean Air Act.
AK-225 (HCFC-225) is a cleaning solvent mixture of two isomers, HCFC-225ca and HCFC-225cb. AK-225 has many unique properties, including its ability to form azeotropes, strong solvency, and thermal stability, which makes it good for use in vapor degreasing. AK-225 is non-flammable, has a low acute toxicity, low viscosity, high density, and low surface tension. This list of great performance characteristics is what makes AK-225 such a great general-purpose precision-cleaning solvent. It is also why this particular solvent has been so difficult to replace with alternatives.
The Agency has approved more than 300 substitutes for multiple applications. Potential substitutes for AK-225 include DuPont Vertrel Solvents (Vertrel XF), n-Propyl Bromide (nPB), Trichloroethylene (TCE; mostly Chinese sources today), 3M hydrofluoroethers (HFEs), and Honeywell's Solstice Performance Fluid (Solstice PF).
DuPont's Vertrel has characteristics similar to AK-225, but is much more environmentally friendly. Solvents containing nPB work well for difficult precision-cleaning applications, but they are not considered environmentally friendly. From a health and environmental perspective, both nPB and TCE are not good replacements for AK-225 due to their low exposure limits and suspect carcinogenicity. The EPA is also currently evaluating the flammability limits of nPB. Additionally, TCE is an overly aggressive solvent making it unsuitable for use with most plastics and elastomers.
From an environmental standpoint 3M HFEs are great as they have been granted VOC exemption. Honeywell's HFO-1233zd(E) has a low global warming potential and is non-flammable. However, cost to the end-user for familiar cleaning applications may be an issue.
Because AK-225 is commonly used in high-end, Class 3 applications (like aerospace, medical, and biotech), qualification of replacement solvents is a difficult and complex process. It is not too early to start the process, and there are many choices to meet most every requirement. ACL Staticide has encouraged its end-use customers to initiate the replacement qualification process early to ensure solvent compatibility, performance, and product availability.
Considering all the facts and chemical replacement requirements from the EPA, ACL has developed a line of solvent chemistries and formulations designed specifically as AK-225 replacements. Our new line includes both flammable products and non-flammable products with our non-flammable alternatives developed specifically for AK-225. In particular, our new ACL 8624 A4 All Purpose Flux Remover & Cleaner has been formulated as a universal performance replacement for all former AK-225 applications. It has many of the same great features of AK-225, but without the ozone-depletion potential. It is recommended that the product be tested on plastics prior to use to determine plastic compatibility with each customer's unique application and process. Contact Q Source, Inc., your ACL Staticide distributor, at 800-966-6020 for more information regarding ACL's AK-225 replacements.
A big thank you to Steve, for another informative Guest Blog. We've appreciated your Q Source Resource contributions throughout this year and we look forward to more in 2015.
For information about ACL Staticide, or to purchase their related products, please visit our ACL Staticide Department at QSource.com. You may also contact us via email or phone (800-966-6020) and one of our associates will be happy to assist you.
For additional Q Source product information, reviews, how-to articles, and special offers please subscribe to our email newsletter.
Friday, December 12, 2014
An Update on the HCFC-225 (AK-225) Phase Out & Ban – Guest Blog
Labels:
ACL Staticide,
AK-225,
Clean Air Act,
EPA,
Guest Blog,
HCFC-225,
ozone-depleting,
ozone-safe,
PCB cleaning,
rework,
Steve Allen
Friday, December 5, 2014
3M 701 Test Kit for Static Control Surfaces: “On the Bench” Video
Check out our latest YouTube video featuring Dave Leventhal, our 3M rep, demonstrating the 3M 701 Static Control Test Kit. In this “On the Bench” video, Dave shows us how easy it is to the 701 Kit to accurately test mats and other surfaces.
To purchase the 3M 701 Static Control Test Kit, please visit QSource.com or contact us via phone (800-966-6020) or email. Shop our complete line of 3M products in our 3M Department at QSource.com.
Don't forget to look out for new "On the Bench" videos at QSource.com and on our YouTube channel.
To purchase the 3M 701 Static Control Test Kit, please visit QSource.com or contact us via phone (800-966-6020) or email. Shop our complete line of 3M products in our 3M Department at QSource.com.
Don't forget to look out for new "On the Bench" videos at QSource.com and on our YouTube channel.
Labels:
3M 701 Static Control Test Kit,
David Leventhal,
On the Bench,
Q Source,
qsource.com,
Video,
YouTube
Wednesday, December 3, 2014
Choose the Perfect Chair w/Our Bevco Seating Questionnaire
QSource.com currently offers more than 700 Bevco Ergonomic Seating products (and that number will continue to grow as we add even more Bevco items). Choosing the right chair can be challenging, but we've recently added a new tool to help you find the perfect one: The Bevco Ergonomic Seating Application Questionnaire.
Asking questions such as, "What application will the seating be used in" and "What chair/stool features are important to you for this purchase" the questionnaire will help us to provide you with the best possible seating options for your needs. The questionnaire also helps you determine the proper seat height range and lets you include as many details as possible to truly narrow down your choices.
After you've completed the online questionnaire, and clicked the submit button, your query is emailed to one of our Q Source Bevco Seating Experts. We will review your request and contact you as soon as possible with options specifically chosen to meet your needs.
As mentioned, our Bevco Ergonomic Seating Department offers more than 700 seating products for purchase. And if you need a little help with your purchase, just click over to the Questionnaire and we'll be happy to assist you. You may also contact us via our Web site, by phone (800-966-6020), or by email.
If there's topic you'd like to see us write about please let us know. We'd also appreciate if you’d share our blog posts with your friends and colleagues and leave us your questions or comments, when applicable. You can follow Q Source on various social media networks including Twitter, Facebook & Google+.
For additional Q Source news, product information, reviews, how-to articles, and special offers please subscribe to our email newsletter and to The Q Source Resource Blog.
Asking questions such as, "What application will the seating be used in" and "What chair/stool features are important to you for this purchase" the questionnaire will help us to provide you with the best possible seating options for your needs. The questionnaire also helps you determine the proper seat height range and lets you include as many details as possible to truly narrow down your choices.
After you've completed the online questionnaire, and clicked the submit button, your query is emailed to one of our Q Source Bevco Seating Experts. We will review your request and contact you as soon as possible with options specifically chosen to meet your needs.
As mentioned, our Bevco Ergonomic Seating Department offers more than 700 seating products for purchase. And if you need a little help with your purchase, just click over to the Questionnaire and we'll be happy to assist you. You may also contact us via our Web site, by phone (800-966-6020), or by email.
If there's topic you'd like to see us write about please let us know. We'd also appreciate if you’d share our blog posts with your friends and colleagues and leave us your questions or comments, when applicable. You can follow Q Source on various social media networks including Twitter, Facebook & Google+.
For additional Q Source news, product information, reviews, how-to articles, and special offers please subscribe to our email newsletter and to The Q Source Resource Blog.
RELATED ARTICLES
Labels:
Bevco Ergonomic Seating,
chairs,
ergonomic chairs and seating,
Industrial Seating,
qsource.com,
questionnaire,
stools
Thursday, November 20, 2014
3M 701 Static Control Test Kit on Flickr
Our 3M rep, Dave Leventhal, stopped by Q Source the other day to demo 3M’s 701 Static Control Test Kit. In addition to making a video of the demo (available on our YouTube Channel), we also snapped a few pics to share with you. The 3M 701 includes all of the items needed to simply and accurately test mats and other surfaces. Check out our latest Flickr photo set for a closer look.
To purchase the 701 Test Kit please visit QSource.com.
To purchase the 701 Test Kit please visit QSource.com.
Labels:
3M 701 Static Control Test Kit,
David Leventhal,
demo,
Flickr,
mats,
photostream,
YouTube
Wednesday, November 19, 2014
Bevco 9000 Series Added to QSource.com: Top-Quality Chairs w/Numerous Options
Bevco's 9000 Series features adjustable backrests with lumbar support, pneumatic height adjustment, 360º swivel, and 300-lb. weight capacity as standard specs. Depending on the model, there are options based on cleanroom class, height adjustment range, color, material, and type of glides. Visit our Web site or contact us for assistance with building seating solutions to meet your needs.
To purchase your Bevco 9000 Series Chairs, please visit the 9000 Series Department at QSource.com or visit the Bevco Ergonomic Seating page for our full selection of Bevco products. You may also contact us via our Web site, by phone (800-966-6020), or by email.
If there's a product or topic you'd like to see The Q Source Resource write about please let us know. We'd also appreciate if you share this blog post with your friends and colleagues via the social media links below. If you have questions or comments about these exclusive Bevco Ergonomic Seating products, please either leave us a message in the comments section or contact us directly.
For additional Q Source product information, reviews, how-to articles, and special offers please subscribe to our email newsletter.
RELATED ARTICLE
Labels:
9000 Series,
Bevco Ergonomic Seating,
cleanroom chairs,
ESD-safe chairs,
Q Source Resource,
qsource.com
Thursday, November 6, 2014
3M’s 724 Dual-Wire Workstation Monitoring Kits: All You Need to Create a Static-Safe Workstation
These two kits (identical other than the color of the included table mat) offer a ready-to-use monitoring solution that as all you need to create and maintain a static-safe workstation. The 3M 724K-WM10 724 Dual-Wire Workstation Monitoring Kit w/Gray 8810 Mat and 724K-WM11 724 Dual-Wire Workstation Monitoring Kit w/Blue 8811 Mat include the following:
- 724 Dual-Wire Workstation Monitor
- 2368 Dual-Wire Fabric Wrist Band for Monitors
- 2360 Dual-Conductor 5’ Ground Cord
- 8810 or 8811 Dissipative Rubber Table Mat in gray or blue, respectively
For additional Q Source product information, reviews, how-to articles, and special offers please subscribe to our email newsletter.
Labels:
3M,
724 Dual-Wire Workstation Monitoring Kits,
724K-WM10,
724K-WM11,
Static Control,
workstation monitor
Wednesday, November 5, 2014
More About the Basics of Flux in Electronics Soldering – Guest Blog
by Steve Allen, VP Marketing and Innovation, ACL Staticide
Steve Allen, from ACL, is back with a further discussion of the basics of flux in electronics soldering
For those of us associated with the electronics manufacturing industry, we are well aware that solder flux is a very important part of the soldering process. Flux is necessary to reduce the oxides that tend to form whenever you have hot metals in contact with the air. In electronics, we use a rosin-core solder, a mild no-clean solder, a more aggressive lead-free solder, or a water-soluble solder to aid the soldering process and eliminate metal oxides. We take great care regarding flux to make sure that we have selected a product that's not plumbing flux or acid-core flux because we know that will tend to corrode parts and components over time; they're okay for pipes but not for electronics.
In many cases, we're looking at rosin solder flux (in paste form) for most applications. If the temperature's a little bit colder, it will tend to crystallize and solidify. But it can be melted with a little bit of heat from the soldering iron. Of course, when you heat flux it tends to produce smoke, so it's good to have ventilation or a fume extractor to be sure that you're not breathing in the caustic vapors created from heating the flux. When you heat a work piece, flux reacts with the metal oxides that are forming with the temperature and exposure to the air. These residual metal oxides tend to interfere with the metal-forming process of soldering. Flux will chemically react with these oxides to make a nice, clean metal from the solder forming process that will form a pristine alloy on the board.
As we know, many solders come with flux in the core. The solder is actually hollow and inside the solder wire there is a central core of flux. As you feed the solder into your work piece, the flux then distributes itself over the surface of the work, reducing the formation of metal oxides and preventing them from occurring during soldering. Flux core solder can be helpful in many soldering instances for small, specific solder and repair projects. Additionally, we should talk about water-soluble flux, which is a recent and significant improvement in flux. With water-soluble flux, cleaning becomes easier. With rosin-core flux, the flux is not water-soluble. It takes an aggressive solvent cleaner to dissolve it and to remove it from the work piece. While easier to clean, water-soluble flux may not be appropriate in all circumstances. It can leave a residual layer that may interfere with high-impedance and high-resistance circuits where you have resistances (10 mega-ohms or greater). The water-based flux may actually lower that resistance and cause the circuit to malfunction.
Solder flux is an essential element when soldering, as it makes the soldering project much easier and of higher quality. Unfortunately, leaving even the no-clean fluxes behind on a PCB can cause some serious issues in circuit performance and even disable components. As part of the basics of flux, it's important that we understand what leaving flux on a PCB can do to your circuit.
In many instances, no-clean flux may not need to be cleaned from a circuit to prevent the flux from physically destroying the circuit. Unfortunately, the presence of flux changes the capacitance between traces, conductive pins, and circuits, and can ultimately get into the mechanical workings of electromechanical components and bind them up. Flux that requires cleaning is very acidic and can eat away at traces and pins, changing their resistance and even destroying surface mount components if the flux is left in place too long.
One particular location in board rework and repair, where the direct presence of residual flux has a significant impact, is on or near the input circuits to a differential input. Differential inputs are often balanced and used for very precise measurements. The presence of flux here will not only throw off any measurement, but can cause the readings to drift significantly over time.
Electromechanical components are also significantly impacted by flux. Often these components are soldered in by hand in the first few prototypes. The hand soldering of these components often works just fine, and the circuit moves on to an initial low-rate production run where problems start to occur in switches and other “mechanical-based” components. Often what happens is that the change in flux application techniques causes flux residue to build up inside the mechanical component and either prevents it from physically moving or makes the switch work intermittently. Troubleshooting these problems is extremely difficult and can lead to significant time loss during troubleshooting. This leads to quality problems we are trying to prevent.
Often when making prototypes components will be hand-soldered in place, circuits will be modified during testing, and parts will be replaced. Each of these operations requires the use of flux, which will need to be cleaned. ACL has developed a complete line of flux removers for all of these specific applications.
No Cleaning – If the circuit is slow, not susceptible to noise errors or increased DC offsets, then no cleaning could work just fine. However, for most circuits leaving the solder flux on the board will cause errors and make troubleshooting much more difficult.
Hand Cleaning – Better than no cleaning at all. Circuits see faster warmup periods and less current offset issues.
Soaking in an Aerosol Solvent Spray – Similar to hand cleaning, aerosol soak and rinse methods can be very helpful in cleaning out mechanical components where hand cleaning simply can't reach.
While it is tempting to save the 10 minutes or so and not perform a proper cleaning, for precision circuits, cleaning is an essential step in the testing and manufacturing process. Keeping a PCB board free of flux build up will save countless days in the testing and troubleshooting process and significantly reduce the stress of tracking down random errors and quality problems. Invest the money and time in an effective cleaner and cleaning process and spend more time building and designing great circuits (rather than countless hours troubleshooting problems).
Thanks Steve, for yet another Guest Blog full of must-have info that our Q Source Resource readers can apply to their own work environments.
For information about ACL Staticide and their related products, please visit our ACL Staticide Department at QSource.com.
For additional Q Source product information, reviews, how-to articles, and special offers please subscribe to our email newsletter.
Steve Allen, from ACL, is back with a further discussion of the basics of flux in electronics soldering
For those of us associated with the electronics manufacturing industry, we are well aware that solder flux is a very important part of the soldering process. Flux is necessary to reduce the oxides that tend to form whenever you have hot metals in contact with the air. In electronics, we use a rosin-core solder, a mild no-clean solder, a more aggressive lead-free solder, or a water-soluble solder to aid the soldering process and eliminate metal oxides. We take great care regarding flux to make sure that we have selected a product that's not plumbing flux or acid-core flux because we know that will tend to corrode parts and components over time; they're okay for pipes but not for electronics.
In many cases, we're looking at rosin solder flux (in paste form) for most applications. If the temperature's a little bit colder, it will tend to crystallize and solidify. But it can be melted with a little bit of heat from the soldering iron. Of course, when you heat flux it tends to produce smoke, so it's good to have ventilation or a fume extractor to be sure that you're not breathing in the caustic vapors created from heating the flux. When you heat a work piece, flux reacts with the metal oxides that are forming with the temperature and exposure to the air. These residual metal oxides tend to interfere with the metal-forming process of soldering. Flux will chemically react with these oxides to make a nice, clean metal from the solder forming process that will form a pristine alloy on the board.
As we know, many solders come with flux in the core. The solder is actually hollow and inside the solder wire there is a central core of flux. As you feed the solder into your work piece, the flux then distributes itself over the surface of the work, reducing the formation of metal oxides and preventing them from occurring during soldering. Flux core solder can be helpful in many soldering instances for small, specific solder and repair projects. Additionally, we should talk about water-soluble flux, which is a recent and significant improvement in flux. With water-soluble flux, cleaning becomes easier. With rosin-core flux, the flux is not water-soluble. It takes an aggressive solvent cleaner to dissolve it and to remove it from the work piece. While easier to clean, water-soluble flux may not be appropriate in all circumstances. It can leave a residual layer that may interfere with high-impedance and high-resistance circuits where you have resistances (10 mega-ohms or greater). The water-based flux may actually lower that resistance and cause the circuit to malfunction.
Solder flux is an essential element when soldering, as it makes the soldering project much easier and of higher quality. Unfortunately, leaving even the no-clean fluxes behind on a PCB can cause some serious issues in circuit performance and even disable components. As part of the basics of flux, it's important that we understand what leaving flux on a PCB can do to your circuit.
![]() |
Leaving fluxes behind can seriously damage a PCB. |
In many instances, no-clean flux may not need to be cleaned from a circuit to prevent the flux from physically destroying the circuit. Unfortunately, the presence of flux changes the capacitance between traces, conductive pins, and circuits, and can ultimately get into the mechanical workings of electromechanical components and bind them up. Flux that requires cleaning is very acidic and can eat away at traces and pins, changing their resistance and even destroying surface mount components if the flux is left in place too long.
One particular location in board rework and repair, where the direct presence of residual flux has a significant impact, is on or near the input circuits to a differential input. Differential inputs are often balanced and used for very precise measurements. The presence of flux here will not only throw off any measurement, but can cause the readings to drift significantly over time.
Electromechanical components are also significantly impacted by flux. Often these components are soldered in by hand in the first few prototypes. The hand soldering of these components often works just fine, and the circuit moves on to an initial low-rate production run where problems start to occur in switches and other “mechanical-based” components. Often what happens is that the change in flux application techniques causes flux residue to build up inside the mechanical component and either prevents it from physically moving or makes the switch work intermittently. Troubleshooting these problems is extremely difficult and can lead to significant time loss during troubleshooting. This leads to quality problems we are trying to prevent.
Often when making prototypes components will be hand-soldered in place, circuits will be modified during testing, and parts will be replaced. Each of these operations requires the use of flux, which will need to be cleaned. ACL has developed a complete line of flux removers for all of these specific applications.
No Cleaning – If the circuit is slow, not susceptible to noise errors or increased DC offsets, then no cleaning could work just fine. However, for most circuits leaving the solder flux on the board will cause errors and make troubleshooting much more difficult.
Hand Cleaning – Better than no cleaning at all. Circuits see faster warmup periods and less current offset issues.
Soaking in an Aerosol Solvent Spray – Similar to hand cleaning, aerosol soak and rinse methods can be very helpful in cleaning out mechanical components where hand cleaning simply can't reach.
While it is tempting to save the 10 minutes or so and not perform a proper cleaning, for precision circuits, cleaning is an essential step in the testing and manufacturing process. Keeping a PCB board free of flux build up will save countless days in the testing and troubleshooting process and significantly reduce the stress of tracking down random errors and quality problems. Invest the money and time in an effective cleaner and cleaning process and spend more time building and designing great circuits (rather than countless hours troubleshooting problems).
Thanks Steve, for yet another Guest Blog full of must-have info that our Q Source Resource readers can apply to their own work environments.
For information about ACL Staticide and their related products, please visit our ACL Staticide Department at QSource.com.
For additional Q Source product information, reviews, how-to articles, and special offers please subscribe to our email newsletter.
Labels:
ACL Staticide,
flux remover,
Guest Blog,
metal oxides,
no-clean flux,
PCB cleaning,
resin-based flux,
soldering,
Steve Allen,
water-soluble flux
Thursday, August 28, 2014
Ensure Workplace Safety, Lean Efficiency w/Ergomat's DuraStripe Floor Marking Solutions
Is your workplace safe? Are potential danger areas clearly marked? If the lights went out would your employees be able to find their way to an exit? Ensure a "yes" answer to all of those questions with Ergomat's DuraStripe line of floor marking shapes, labels, tapes, and signs.
QSource.com recently added hundreds of these items from a number of Ergomat's popular DuraStripe lines (including DuraStripe Glow, Mean Lean, Supreme V, and X-Treme). By introducing these visual indicators, your employees will be better aware of proper procedures and better prepared to navigate the workplace safely.
Lead them through the darkness with DuraStripe Glow, the peel and stick floor/aisle marking tape. Made of glow-in-the-dark material, this durable tape is quick and easy to install and requires no dry or cure time. Available with or without text and in a choice of widths for the glow line.

All of the aforementioned DuraStripe products include a two-year warranty and are available in a number of dimensions, colors, and shapes. Please visit QSource.com for further information.
For additional Q Source product information, reviews, how-to articles, and special offers please subscribe to our email newsletter.
QSource.com recently added hundreds of these items from a number of Ergomat's popular DuraStripe lines (including DuraStripe Glow, Mean Lean, Supreme V, and X-Treme). By introducing these visual indicators, your employees will be better aware of proper procedures and better prepared to navigate the workplace safely.
DURASTRIPE GLOW

DURASTRIPE MEAN LEAN
Have your employees literally follow the footsteps to workplace efficiency and safety. The economical, low-profile DuraStripe Mean Lean shapes and tapes are great for Visual Workplace, 5S, and Lean applications, aisle striping, and come in a variety of shapes (including arrows, circles, letters, numbers, and yes, even footprints) and seven standard colors. This durable material is easy to clean and remove, scuff-resistant, and requires no messy cleanup.DURASTRIPE SUPREME V
For a long-lasting floor-marking solution, Ergomat has combined their original DuraStripe material with their DuraStripe Lean to create a fifth-generation product: DuraStripe Supreme V. Supreme V mixes the original DuraStripe adhesive with DuraStripe Lean's low profile to make a product perfect for use in almost any environment and a superior option for imperfect floor conditions. DuraStripe Supreme V features tapered edges to deter possible tripping and impact dangers, is available in a variety of shapes (including triangles, corners, pluses, squares, and pedestrians), colors, and sizes; and is easy to install.
DURASTRIPE X-TREME
For those extreme, critical environments where forklift/tow motors are in frequent use, check out the heavy-duty DuraStripe X-Treme line of floor-marking products. DuraStripe X-Treme features a specially coated surface (for easy cleaning) and beveled edges to deter damages to the material. This durable DuraStripe line is also ideal for Lean applications (such as Six Sigma, 5S, etc.) and is available in a number of widths, colors, and shapes (including curves, strips, t-shapes, double-sided arrows, and pux).All of the aforementioned DuraStripe products include a two-year warranty and are available in a number of dimensions, colors, and shapes. Please visit QSource.com for further information.
For additional Q Source product information, reviews, how-to articles, and special offers please subscribe to our email newsletter.
Labels:
5S,
DuraStripe,
DuraStripe Glow,
DuraStripe Mean Lean,
DuraStripe Supreme V,
DuraStripe X-Treme,
Ergomat,
floor striping,
Six Sigma,
visual workplace,
worker safety
Tuesday, July 29, 2014
ACL Staticide Flux Removers: “On the Bench” Video
ACL Staticide's VP of Marketing & Innovation and Q Source Guest Blogger, Steve Allen, paid us a visit to provide an overview of ACL's new aerosol cleaning products. In this "On the Bench" video, Steve talks about flux removers.
Focusing on ACL's Flux Remover No Clean, Flux Remover Lead-Free, Flux Remover Rosin, and Flux Remover Heavy Duty, Steve tells us about the need for flux removers and then demonstrates ACL's recommended cleaning process.
To purchase ACL Staticide Flux Removers, please visit QSource.com or contact us via phone (800-966-6020) or email. Shop our complete line of ACL products at our ACL Staticide Department at QSource.com.
Don't forget to look out for new "On the Bench" videos at QSource.com and on our YouTube channel.
Focusing on ACL's Flux Remover No Clean, Flux Remover Lead-Free, Flux Remover Rosin, and Flux Remover Heavy Duty, Steve tells us about the need for flux removers and then demonstrates ACL's recommended cleaning process.
To purchase ACL Staticide Flux Removers, please visit QSource.com or contact us via phone (800-966-6020) or email. Shop our complete line of ACL products at our ACL Staticide Department at QSource.com.
Don't forget to look out for new "On the Bench" videos at QSource.com and on our YouTube channel.
Thursday, July 24, 2014
New Atrix Vacuums, Kit Add LED Indicator Light for Safer Operation
Atrix International has released new vacuums and an add-on kit featuring an indicator light to warn of potential filter overflows. Aimed at providing a safety feature to avoid hazardous materials overflowing from the vacuum filter, the new indicator light is available on the Atrix VACHFIL Omega Plus Abatement Vacuum w/HEPA Filter & Light Kit, VACGFIL Omega Green Supreme Vacuum w/HEPA Filter & Light Kit, and as the FILKIT Full Filter Indicator Light Kit for Omega Series & High-Capacity Vacuums.
The red LED filter indicator light warns when the filter is reaching full capacity, helping you avoid potential dangers of materials like lead dust, mold spores, asbestos, etc. escaping from the filter. Changing the filter at the right time will also protect the lifespan of the vacuum, save on filter costs, and boost filter efficiency.
Specifications
According to Atrix, the ESD-safe Omega Green Supreme Vacuum is the quietest, most powerful service vacuum available. Made from long-lasting, high-impact starex flame retardant ABS polymer, the VACGFIL's new motor uses 20% less energy, and its HEPA Filter is 99.97%. As with the VACHFIL, the Filter Full Indicator Light complies with British Standard No. 8520. Included with the VACGFIL Omega Green Supreme are a 6' ESD-safe crush-proof stretch hose, 16" ESD-safe flexible wand, and a Shoulder strap.
Specifications
FILKIT FULL FILTER INDICATOR LIGHT KIT FOR OMEGA SERIES & HIGH-CAPACITY VACUUMS
The FILKIT Full Filter Indicator Kit allows the Omega Plus, Omega Supreme Plus, Omega Green Series, Omega MRI Series and Omega Cleanroom Series Vacuums to be equipped with the new red LED warning light. As previously mentioned, the light illuminates as the filter approaches full capacity and meets British Standard Number 8520, which applies to all fine-filtered HEPA and ULPA vacuums used with hazardous materials. Please note: The FILKIT must be ordered at the time of purchase of an Omega Series or High-Capacity Vacuums.
The VACHFIL, VACGFIL, and FILKIT are all available at QSource.com and can be ordered online, via email, or by calling us at 800-966-6020. For a complete selection of Atrix products, please visit our Atrix International Department.
For additional Q Source product information, reviews, how-to articles, and special offers please subscribe to our email newsletter.
The red LED filter indicator light warns when the filter is reaching full capacity, helping you avoid potential dangers of materials like lead dust, mold spores, asbestos, etc. escaping from the filter. Changing the filter at the right time will also protect the lifespan of the vacuum, save on filter costs, and boost filter efficiency.
![]() |
Atrix VACHFIL Omega Plus Abatement Vacuum |
VACHFIL OMEGA PLUS ABATEMENT VACUUM W/HEPA FILTER & LIGHT KIT
This portable Omega Plus Vacuum is made of durable, high-impact Starex flame-retardant polymer, has built-in over-heat protection, and features a self-contained HEPA filter cartridge that traps hazardous particulates. The Filter Full Indicator Light complies with British Standard No. 8520. The quiet, yet powerful, VACHFIL includes a hose plug, utility nozzle, utility brush, 6' clear hose, crevice tool/brush, and 16" flexible wand.Specifications
- 120-Volt Motor: 5.2 Amps, 628 Watts (a 230-Volt Motor: 2.0 Amps, 450 Watts model is also available)
- 19.25" Length
- 7.4" Width
- 9.3" Height
- 11 lb. Weight
VACGFIL OMEGA GREEN SUPREME VACUUM W/HEPA FILTER & LIGHT KIT
![]() |
Atrix VACGFIL Omega Green Supreme Vacuum (Arrow points out the new LED indicator light.) |
Specifications
- 120-Volt Motor: 5.2 Amps, 628 Watts (a 230-Volt Motor: 2.0 Amps, 450 Watts is also available)
- 19.25” Length
- 7.4” Width
- 9.3” Height
- 11 lb. Weight
![]() |
Atrix FILKIT Full Filter Indicator Kit |
The FILKIT Full Filter Indicator Kit allows the Omega Plus, Omega Supreme Plus, Omega Green Series, Omega MRI Series and Omega Cleanroom Series Vacuums to be equipped with the new red LED warning light. As previously mentioned, the light illuminates as the filter approaches full capacity and meets British Standard Number 8520, which applies to all fine-filtered HEPA and ULPA vacuums used with hazardous materials. Please note: The FILKIT must be ordered at the time of purchase of an Omega Series or High-Capacity Vacuums.
The VACHFIL, VACGFIL, and FILKIT are all available at QSource.com and can be ordered online, via email, or by calling us at 800-966-6020. For a complete selection of Atrix products, please visit our Atrix International Department.
For additional Q Source product information, reviews, how-to articles, and special offers please subscribe to our email newsletter.
Labels:
Atrix International,
FILKIT,
Full Filter Indicator Light Kit,
hazardous particles,
Omega Series Vacuum,
VACGFIL,
VACHFIL
Tuesday, July 22, 2014
New Brady Infographics Focus on Traceability
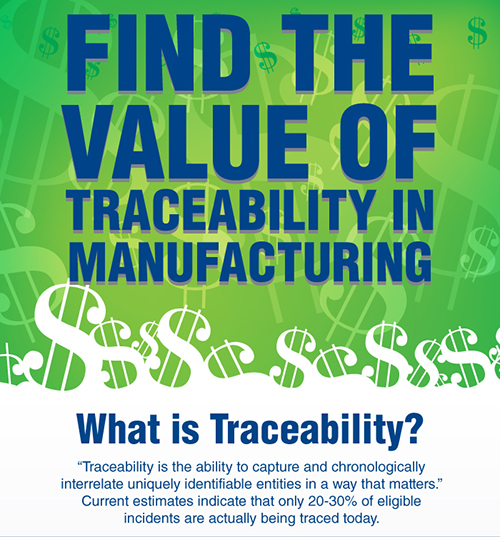
Brady's "FIND THE VALUE OF TRACEABILITY IN MANUFACTURING" focuses on the process you need to take to be able to track a part, product, or component through a manufacturing routine. (Click the image for the complete, full-size graphic.)
The second information-packed infographic, "PCB LABELS: PROPERTIES YOU NEED FOR YOUR PROCESS," provides details about the label properties you will need for a PCB traceability process. (Click the image for the complete, full-size graphic.)

Q Source has been an official distributor for Brady products since 1984. If you have further questions about these products, or need help placing an order, you may also contact us at 800-966-6020 or via email and one of our Brady experts will be happy to assist you.
For additional Q Source product information, reviews, how-to articles, and special offers please subscribe to our email newsletter.
Labels:
Brady,
Infographics,
labeling,
manufacturing,
PCBs,
traceability
Tuesday, July 1, 2014
Andersen Company WaterHog Classic/Fashion Diamond Entrance Mat: "On the Bench" Video
Andersen Company's Mike Andersen stopped by Q Source recently to talk to us about Andersen Mats. In this "On the Bench" video, Mike focuses on the WaterHog Classic/Fashion Diamond Entrance Mat.
These wiper/scraper entrance mats are made of a polypropylene fiber system and SBR rubber backing, which contain 20% recycled rubber.
To purchase WaterHog mats, please visit QSource.com or contact us via phone (800-966-6020) or email. Check out our Andersen Company Department for a complete line of mats.
Don't forget to look out for new "On the Bench" videos at QSource.com and on our YouTube channel.
These wiper/scraper entrance mats are made of a polypropylene fiber system and SBR rubber backing, which contain 20% recycled rubber.
To purchase WaterHog mats, please visit QSource.com or contact us via phone (800-966-6020) or email. Check out our Andersen Company Department for a complete line of mats.
Don't forget to look out for new "On the Bench" videos at QSource.com and on our YouTube channel.
Labels:
Andersen Company Mats,
Mike Andersen,
On the Bench,
polypropylene,
Q Source,
Waterhog,
YouTube
Wednesday, June 11, 2014
How to Use the 80:20 Rule to Focus on the Business Innovation Process - Guest Blog
by Steve Allen, VP Marketing and Innovation, ACL Staticide
Our guest blogger, Steve Allen from ACL, looks at how to apply the Pareto Principle’s 80:20 rule in your business practices
"There is nothing quite so useless, as doing with great efficiency, something that should not be done at all."—Peter Drucker
The Pareto Principle (also known as the 80:20 rule), irrespective of the nature of your business, holds that 80% of the consequences of any action come from 20% of the causes. This principle can actually be applied to everything you do. At ACL, we implement 80:20 simplification and rationalization disciplines into everything we do, including new product development and commercialization.
The original 80:20 observation is attributed to Italian economist Vilfredo Pareto who, in 1906, noticed that 80% of Italy's land was owned by 20% of the population. He then carried out surveys on a variety of other countries and found to his surprise that a similar distribution applied. He and others later discovered that this principle is proven in many other areas of interest:
The same is true of time expended for results achieved. Think of the benefits of applying the Pareto Principle to your time management and personal and business productivity!
Which one of these statements rings true for your business?
The common approach to business is to squeeze every last drop out of each opportunity, to go "100% all-out," without consideration of the impact on time, productivity, and waste. Simple, time-efficient businesses recognize that it is fundamentally inefficient to go for the "whole pie" when you can get the majority of results for the minority of effort. With knowledge of the 80:20 lean simplification principles, you can concentrate on what wins you customers and successes in the most efficient manner and in the shortest amount of time. Look at your business and concentrate on the 20% that produces the 80% of benefit. Spend 80% of your time doing the 20% that really gets you results.
It’s not just about working smarter—it's about working smarter on the right things that will get you the best results. Pareto rules allow us to launch the products we know our customers need (such as the industry top-selling items offered in our new PCB Electronics Rework/Repair Production Chemicals line), and that our key distributor partners and sales teams can effectively sell. 80:20 gives us insight into developing value-added products that solve real problems for our customers.
Q Source, once again, thanks ACL Staticide’s Steve Allen for his Guest Blog contributions to The Q Source Resource.
For information about ACL Staticide products, please visit our ACL Staticide Department at QSource.com. You may also contact us via email or phone at 800-966-6020 and one of our associates will be happy to answer your questions or assist you with an order.
If there's a product or topic you'd like to see The Q Source Resource write about please let us know. We'd also appreciate if you share this blog post with your friends and colleagues via the social media links below. If you have questions or comments about the 80:20 rule or about ACL Staticide products please leave us a message in the comments section.
For additional Q Source product information, reviews, how-to articles, and special offers please subscribe to our email newsletter.
Steve Allen's Previous Guest Blogs
Our guest blogger, Steve Allen from ACL, looks at how to apply the Pareto Principle’s 80:20 rule in your business practices
"There is nothing quite so useless, as doing with great efficiency, something that should not be done at all."—Peter Drucker
![]() |
Italian Economist Vilfredo Pareto |
The original 80:20 observation is attributed to Italian economist Vilfredo Pareto who, in 1906, noticed that 80% of Italy's land was owned by 20% of the population. He then carried out surveys on a variety of other countries and found to his surprise that a similar distribution applied. He and others later discovered that this principle is proven in many other areas of interest:
- 80% of results come from 20% of effort
- 20% of your customers will account for 80% of your profit
- 80% of your sales come from only 20% of your total product line
The same is true of time expended for results achieved. Think of the benefits of applying the Pareto Principle to your time management and personal and business productivity!
Which one of these statements rings true for your business?
- 80% of your business comes from 20% of your customers
- 20% of your product or service range contributes 80% of your sales and likely 90% of profits
- 80% of customer complaints originate from 20% of the causes
- 80% of your business productivity loss results from 20% of the causes
- 80% of the value in the business is generated by 20% of the processes
It’s not just about working smarter—it's about working smarter on the right things that will get you the best results. Pareto rules allow us to launch the products we know our customers need (such as the industry top-selling items offered in our new PCB Electronics Rework/Repair Production Chemicals line), and that our key distributor partners and sales teams can effectively sell. 80:20 gives us insight into developing value-added products that solve real problems for our customers.
Q Source, once again, thanks ACL Staticide’s Steve Allen for his Guest Blog contributions to The Q Source Resource.
For information about ACL Staticide products, please visit our ACL Staticide Department at QSource.com. You may also contact us via email or phone at 800-966-6020 and one of our associates will be happy to answer your questions or assist you with an order.
If there's a product or topic you'd like to see The Q Source Resource write about please let us know. We'd also appreciate if you share this blog post with your friends and colleagues via the social media links below. If you have questions or comments about the 80:20 rule or about ACL Staticide products please leave us a message in the comments section.
For additional Q Source product information, reviews, how-to articles, and special offers please subscribe to our email newsletter.
Steve Allen's Previous Guest Blogs
Labels:
80:20 rule,
ACL Staticide,
business productivity,
Guest Blog,
Italian economist,
Pareto Principle,
PCB cleaning,
Peter Drucker,
Steve Allen
Thursday, June 5, 2014
Dazor J203HHM Mini Hand-Held Portable Magnifier on Flickr
The Dazor J203HHM Mini Hand-Held Portable Magnifier is a fast and easy inspection tool that provides hands-free operation and distortion-free viewing. This magnifier features LED lights, 50,000 hours of service, a built-in stand, and a carrying case. Check out our Flickr photo set to get a closer look at Dazor’s J203HHM.
To purchase this Dazor Mini Hand-Held Portable Magnifier please visit QSource.com.
To purchase this Dazor Mini Hand-Held Portable Magnifier please visit QSource.com.
Wednesday, May 28, 2014
Weller WD1M WD Series Micro Digital Rework Station on Flickr
The Weller WD1M WD Series Micro Digital Rework Station is ESD safe and features an extensive special functions menu, large, high-contrast LCD display; and three "radio buttons" for pre-setting frequently used temperatures. Check out our Flickr photo set to get a closer look at this Weller Rework Station.
To purchase the Weller WD1M WD Series Micro Digital Rework Station please visit QSource.com.
To purchase the Weller WD1M WD Series Micro Digital Rework Station please visit QSource.com.
Labels:
ESD-Safe,
Flickr,
LCD display,
pre-set temperatures,
WD Series,
Weller WD1M Micro Digital Rework Station
Wednesday, May 21, 2014
Steinel 34750 HB 1750 Heat Blower w/5 Temperature Keys on Flickr
The Steinel 34750 HB 1750 Heat Blower w/5 Temperature Keys is an ergonomic, ultra-quiet, advanced high-output blower. This high-quality heat blower features a powerful turbine blower, maintenance-free factory sealed motor, soft grip handle with convenient slide switch, and color-coded temperature keys. Check out our Flickr photo set to get a closer look at the Steinel HB 1750 Heat Blower.
To purchase this item please visit our Web site.
To purchase this item please visit our Web site.
Tuesday, May 13, 2014
Hakko's New FM-2032 Micro Soldering Iron, T-30 Tips Now at QSource.com
American Hakko (Hakko) has released their new FM-2032 Micro Soldering Iron. In addition, a related conversion kit and several new T-30 Series tips are also now available at QSource.com.
The Hakko FM-2032 is a thin, lightweight handpiece that provides a precision micro soldering option to a variety of Hakko Soldering and Rework Systems. The ESD-safe FM-2032 was created for working with 0201 components or smaller and features an optimized tip-to-grip distance for operator dexterity and control under microscopes and magnifiers. The grip stays cool even when running at 450° C for extended periods of time and the thin iron cord is burn resistant.
Let's take a look at the FM-2032 Micro Soldering Iron's specifications:
The FM-2032 uses Hakko's new T-30 Series Composite Micro Tips. These quick-change tips feature geometries engineered for optimal heat transfer and can reach into many of the tightest spots on a board. These T-30 Tips incorporate Hakko’s well-known tip life and performance characteristics. Please Note: The FM-2032 does not include any soldering tips or accessories.
The following T-30 Series Tips are now available at QSource.com:
Hakko has also released a Micro Soldering Iron Conversion Kit (FM2032-52), which allows the FM-2032 to be used with Hakko's FX-951 Soldering Station, FM-203 Dual Port Soldering System w/FM2027-03 Handpiece, and FM-206 3-Port Rework Station. The kit contains the FM-2032 Micro Soldering Iron, the Iron Holder, a Heat-Resistant Pad, and a Connecting Cable.
To place an order for the Hakko FM-2032 Micro Soldering Iron, T-30 Tips, or FM2032-52 Conversion Kit please visit our FM2032 Micro Soldering Iron Page at QSource.com or contact us via phone (800-966-6020) or email. Please check back soon for information about other new Hakko products.
If there's a product or topic you'd like to see The Q Source Resource write about please let us know. We'd also appreciate if you share this blog post with your friends and colleagues via the social media links below. If you have questions or comments about anything on The Q Source Resource or QSource.com please leave us a message in the comments section.
For additional Q Source product information, reviews, how-to articles, and special offers please subscribe to our email newsletter.
RELATED ARTICLES
The Hakko FM-2032 is a thin, lightweight handpiece that provides a precision micro soldering option to a variety of Hakko Soldering and Rework Systems. The ESD-safe FM-2032 was created for working with 0201 components or smaller and features an optimized tip-to-grip distance for operator dexterity and control under microscopes and magnifiers. The grip stays cool even when running at 450° C for extended periods of time and the thin iron cord is burn resistant.
Let's take a look at the FM-2032 Micro Soldering Iron's specifications:
- Power consumption: 48W / 24V
- Temperature range: 400° - 840°F (200° - 450°C)
- Tip-to-Ground resistance: < 2 ohms
- Tip-to-Ground potential: < 2mV
- Temperature accuracy: Meets or Exceeds IPC J-STD-001 with Offset
- Temperature stability: ±5.5°F (±3°C)
- ESD properties: ESD-safe
- Reach: 3.9' (1.2 m)
- Handpiece length: 6.7" (170 mm) w/T30-D1 tip
- Weight of handpiece: 0.49 oz (14 g) w/T30-D1 tip
- Tip-to-ground distance: ~1.97" (50 mm)
- Grip diameter: 0.45" (11.6 mm)
- Acceptable tips: T-30 Series (not included)
- Tip diameter: 0.130" (3.3 mm)
NEW IRON, NEW TIPS
The FM-2032 uses Hakko's new T-30 Series Composite Micro Tips. These quick-change tips feature geometries engineered for optimal heat transfer and can reach into many of the tightest spots on a board. These T-30 Tips incorporate Hakko’s well-known tip life and performance characteristics. Please Note: The FM-2032 does not include any soldering tips or accessories.
The following T-30 Series Tips are now available at QSource.com:
- T30-D06 T-30 Series Micro Soldering Tip - Chisel - 6 x 0.6 mm
- T30-D1 T-30 Series Micro Soldering Tip - Chisel - 6.5 x 1 mm
- T30-I T-30 Series Micro Soldering Tip - Conical - 6 mm
- T30-J T-30 Series Micro Soldering Tip - Bent - 40° - 6 mm
- T30-KN T-30 Series Micro Soldering Tip - Knife - 45° - 8.5 x 1.4 mm
- T30-KU T-30 Series Micro Soldering Tip - Knife - 45° - 6 x 1.8 mm
VERSATILITY IN A KIT

To place an order for the Hakko FM-2032 Micro Soldering Iron, T-30 Tips, or FM2032-52 Conversion Kit please visit our FM2032 Micro Soldering Iron Page at QSource.com or contact us via phone (800-966-6020) or email. Please check back soon for information about other new Hakko products.
If there's a product or topic you'd like to see The Q Source Resource write about please let us know. We'd also appreciate if you share this blog post with your friends and colleagues via the social media links below. If you have questions or comments about anything on The Q Source Resource or QSource.com please leave us a message in the comments section.
For additional Q Source product information, reviews, how-to articles, and special offers please subscribe to our email newsletter.
RELATED ARTICLES
Labels:
FM-2032 Micro Soldering Iron,
FM2032-52 Conversion Kit,
Hakko,
New Products,
rework,
soldering,
T-30 Series Composite Micro Tips
Wednesday, May 7, 2014
The Ergonomic Seating Solution: It Makes Dollars and Sense – Guest Blog
by Melinda Bohlmann, Bevco Precision Manufacturing Company
Melinda Bohlmann, our guest blogger from Bevco, writes about the health and financial benefits of providing workers with quality ergonomic seating.
You’ve seen the statistics. A report from the N.C. Department of Labor Occupational Safety and Health Program shows that almost 50% of workers in the industrial space suffer from back problems. Proper sitting contributes to the physical well-being of a worker and may add as much as 40 minutes of production to each workers day. The National Research Council and the Institute of Medicine estimate that nearly 1 million individuals in the United States lose time from work each year due to work-related musculoskeletal disorders (MSDs), with an associated $45-$54 billion annual cost.
The evidence is staggering; the solution is clear. Having employees sit in the proper chair will not only save money (think lost time and medical expenses), but increase worker productivity. Who wouldn’t want that? Yet time after time we hear “I just need the cheapest chair you have.”
Let’s break it down. In this example, a company needs to purchase 100 chairs for their production facility. We’ll estimate that a good ergonomic chair costs $300 and an inexpensive, non-ergonomic chair costs $150. The ergonomic solution will cost $30,000 and the inexpensive solution will cost half that, $15,000. That seems like a lot of money to save, doesn’t it? Remember, looks can be deceiving.
In 2005, the U.S. Department of Labor determined that there were 4.6 injuries per 100 full-time employees in the workplace. Thirty percent of these injuries are due to low-back disorders. Injured employees required an average of 19 therapy visits (Worker’s Compensation Research Institute). A work-related injury resulted in an average loss of approximately $38,000 including wages, productivity loss, and medical expenses (National Safety Council, 2005).
Going back to our example—we’ll say that one employee suffers an MSD at an average loss of $38,000. If the facility went with the inexpensive chair solution they would have not only spent $15,000 for the chairs, but also an additional $38,000 to pay for the cost of the work-related injury—a total of $53,000. If the facility would have gone with the ergonomic solution they could have saved $23,000.
The ergonomic solution saves the most dollars…and makes the most sense. Not only for the bottom line, but also for the comfort and well-being of the employees.
Bevco has been a leading manufacturer of ergonomic seating for more than 60 years. Based in Waukesha, Wisconsin, Bevco offers a comprehensive line of seating for the industrial, laboratory, education, office, sewing, medical, and electronics market. The company is dedicated to providing customers with safe, ergonomic seating solutions that adhere to the highest quality regulations on the market.
Q Source would like to thank our guest blogger, Melinda Bohlmann. We appreciate your contribution to The Q Source Resource.
For additional Q Source product information, reviews, how-to articles, and special offers please subscribe to our email newsletter.
Melinda Bohlmann, our guest blogger from Bevco, writes about the health and financial benefits of providing workers with quality ergonomic seating.
You’ve seen the statistics. A report from the N.C. Department of Labor Occupational Safety and Health Program shows that almost 50% of workers in the industrial space suffer from back problems. Proper sitting contributes to the physical well-being of a worker and may add as much as 40 minutes of production to each workers day. The National Research Council and the Institute of Medicine estimate that nearly 1 million individuals in the United States lose time from work each year due to work-related musculoskeletal disorders (MSDs), with an associated $45-$54 billion annual cost.
![]() |
Bevco offers a wide selection of high-quality ergonomic chairs |
Let’s break it down. In this example, a company needs to purchase 100 chairs for their production facility. We’ll estimate that a good ergonomic chair costs $300 and an inexpensive, non-ergonomic chair costs $150. The ergonomic solution will cost $30,000 and the inexpensive solution will cost half that, $15,000. That seems like a lot of money to save, doesn’t it? Remember, looks can be deceiving.
In 2005, the U.S. Department of Labor determined that there were 4.6 injuries per 100 full-time employees in the workplace. Thirty percent of these injuries are due to low-back disorders. Injured employees required an average of 19 therapy visits (Worker’s Compensation Research Institute). A work-related injury resulted in an average loss of approximately $38,000 including wages, productivity loss, and medical expenses (National Safety Council, 2005).
Going back to our example—we’ll say that one employee suffers an MSD at an average loss of $38,000. If the facility went with the inexpensive chair solution they would have not only spent $15,000 for the chairs, but also an additional $38,000 to pay for the cost of the work-related injury—a total of $53,000. If the facility would have gone with the ergonomic solution they could have saved $23,000.
The ergonomic solution saves the most dollars…and makes the most sense. Not only for the bottom line, but also for the comfort and well-being of the employees.
Bevco has been a leading manufacturer of ergonomic seating for more than 60 years. Based in Waukesha, Wisconsin, Bevco offers a comprehensive line of seating for the industrial, laboratory, education, office, sewing, medical, and electronics market. The company is dedicated to providing customers with safe, ergonomic seating solutions that adhere to the highest quality regulations on the market.
Q Source would like to thank our guest blogger, Melinda Bohlmann. We appreciate your contribution to The Q Source Resource.
For additional Q Source product information, reviews, how-to articles, and special offers please subscribe to our email newsletter.
Wednesday, April 30, 2014
Volatile Organic Compounds & Evolving Regulations – Guest Blog
by Steve Allen, VP Marketing and Innovation, ACL Staticide
Steve Allen, our guest blogger from ACL, this time focuses on the topic of VOCs and aerosol cleaners
An important topic today with end-use customers using aerosol cleaners, is the changing regulations regarding the VOC content and compliance of solvent-based products. Many customers are perplexed as to why manufacturers and suppliers don't already have this information on their product MSDS (GHS safety data sheets) and tech data sheets. At one time, the weight percent of all non-exempt chemicals in most products was listed on each product MSDS, but this information has been removed for several reasons. And, as most everyone knows, the regs are changing all the time.
There is an evolving Federal list of exempt chemicals along with many state and municipal lists of currently exempt chemicals. In some instances, these lists do not always agree. Additionally, there exists at least three EPA-approved ways to calculate VOC content. And, each method can yield different values for the same product. The choice of a particular calculation method can depend on the customer's location and the air quality regulations for their particular region.
It's important to review what a VOC is and why it's important. VOC stands for "volatile organic compound." These are chemicals whose vapors have been found to chemically react with nitrogen oxides (NOx, which are produced by auto exhaust, the burning of fossil fuels for power generation, and other industrial processes) in the air and in the presence of sunlight to produce ground-level ozone or "smog". The ability of certain chemical vapors to produce smog when sunlight makes them react with nitrogen oxides is referred to as photochemical reactivity. The direct emission of these vapors into the air defines the scope with which the EPA is most concerned. Thus, chemicals whose vapors are not photochemically reactive to form smog are considered exempt and are not included in the process of determining the amount of VOC ingredients in a particular product.
The federal EPA publishes a list of exempt chemicals and many states also publish their own list. A chemical that is listed as exempt on the EPA list may not appear on the individual state or municipality listings. A basic Internet search for methods of calculating VOC will generate literally 1000s of information sources and reference sites. VOC test results are used for a variety of purposes. These are predominantly for emissions fees, new source review applicability, and compliance with permit limits.
Most VOC and air quality/emissions permits do not specify VOC test methodology for purposes of demonstrating compliance with VOC limits. Currently, there are inconsistencies and a lack of guidance among states and EPA regions in implementation of VOC test methodology. It is technically difficult to specify any one single method for VOC measurement. This is why it is difficult to specify a simple value for the VOC content of most cleaning products. Without specific knowledge of the area of the country in which the customer is located, the EPA region under whose regulations they operate, if they are operating under a Federal NESHAP, the existence of state and local emission regulations, and the specific application or way in which the product will be used, it is difficult-to-impossible to list accurate and specific VOC information on a product MSDS.
Many states do not recognize all of the chemicals on the EPA lists as being exempt. Formal exemption of a chemical from VOC consideration may depend on how it is being used. California is generally the most extreme case and most industry there is moving toward water-based cleaning.
So, why are VOC determinations mission-critical today? Traditionally, VOCs have been used for conformal coating and various contact cleaning and flux removal applications. The properties of a conformal coating stem from the selected base resin and the various additives, while the solvents used in most cleaners come from an aromatic or aliphatic hydrocarbon base. These are included to optimize the performance of the cured coating or the formulated cleaner. Organic solvents are used to dissolve the base resin and reduce viscosity to bring the coating within a workable range. As such, the conformal coating dries by a simple solvent evaporation. Contact cleaners and flux removers function in the same manner.
Solvent-based conformal coatings are extremely versatile and can be applied in many ways, such as dipping, spraying, and brushing. By simply adjusting the solvent level, the viscosity of the coating can be tailored to the required application method. Solvents or VOCs are used for many different cleaning applications during PCB manufacture. Until recently, there has been a reluctance to change to alternative products for a number of reasons:
Many manufacturers are turning to "no-clean" processes implying that cleaning is not required after soldering. In the "no-clean" process, rosin and activator are not removed prior to the next process such as coating or encapsulating of the PCB. Such residues, along with any other unwanted elements collected due to the missing cleaning stage, could cause issues with adhesion and possibly affect the performance of the protecting media applied. It can therefore be stated that even with advances in new technologies, such as "no-clean" fluxes, cleaning is still an essential multi-stage process within the electronics industry. Finally, there are also cleaning stages required for the removal of coatings and adhesives when re-work is necessary and for the cleaning of actual components and for maintenance of the production line.
Volatile organic compounds in cleaning and coating chemistries will continue to be a point of concern at the end-user level. Low VOC alternatives are available as are water-based options. Every manufacturer must maintain awareness of changing VOC regs and formulate products which are in the best interest of the environment, the industry, and most importantly, the end-use customer. ACL Staticide is committed to this effort as we develop and commercialize industry responsible and compliant new products.
If there's a product or topic you'd like to see The Q Source Resource write about please let us know. We'd also appreciate if you share this blog post with your friends and colleagues via the social media links below. If you have questions or comments about ACL Staticide products or about cleaning printed circuit boards and electronic equipment please leave us a message in the comments section.
For additional Q Source product information, reviews, how-to articles, and special offers please subscribe to our email newsletter.
Steve Allen, our guest blogger from ACL, this time focuses on the topic of VOCs and aerosol cleaners
An important topic today with end-use customers using aerosol cleaners, is the changing regulations regarding the VOC content and compliance of solvent-based products. Many customers are perplexed as to why manufacturers and suppliers don't already have this information on their product MSDS (GHS safety data sheets) and tech data sheets. At one time, the weight percent of all non-exempt chemicals in most products was listed on each product MSDS, but this information has been removed for several reasons. And, as most everyone knows, the regs are changing all the time.
It's important to review what a VOC is and why it's important. VOC stands for "volatile organic compound." These are chemicals whose vapors have been found to chemically react with nitrogen oxides (NOx, which are produced by auto exhaust, the burning of fossil fuels for power generation, and other industrial processes) in the air and in the presence of sunlight to produce ground-level ozone or "smog". The ability of certain chemical vapors to produce smog when sunlight makes them react with nitrogen oxides is referred to as photochemical reactivity. The direct emission of these vapors into the air defines the scope with which the EPA is most concerned. Thus, chemicals whose vapors are not photochemically reactive to form smog are considered exempt and are not included in the process of determining the amount of VOC ingredients in a particular product.
The federal EPA publishes a list of exempt chemicals and many states also publish their own list. A chemical that is listed as exempt on the EPA list may not appear on the individual state or municipality listings. A basic Internet search for methods of calculating VOC will generate literally 1000s of information sources and reference sites. VOC test results are used for a variety of purposes. These are predominantly for emissions fees, new source review applicability, and compliance with permit limits.
Most VOC and air quality/emissions permits do not specify VOC test methodology for purposes of demonstrating compliance with VOC limits. Currently, there are inconsistencies and a lack of guidance among states and EPA regions in implementation of VOC test methodology. It is technically difficult to specify any one single method for VOC measurement. This is why it is difficult to specify a simple value for the VOC content of most cleaning products. Without specific knowledge of the area of the country in which the customer is located, the EPA region under whose regulations they operate, if they are operating under a Federal NESHAP, the existence of state and local emission regulations, and the specific application or way in which the product will be used, it is difficult-to-impossible to list accurate and specific VOC information on a product MSDS.
Many states do not recognize all of the chemicals on the EPA lists as being exempt. Formal exemption of a chemical from VOC consideration may depend on how it is being used. California is generally the most extreme case and most industry there is moving toward water-based cleaning.

Solvent-based conformal coatings are extremely versatile and can be applied in many ways, such as dipping, spraying, and brushing. By simply adjusting the solvent level, the viscosity of the coating can be tailored to the required application method. Solvents or VOCs are used for many different cleaning applications during PCB manufacture. Until recently, there has been a reluctance to change to alternative products for a number of reasons:
- Change required alterations to production procedures and equipment
- Solvent-based materials were very well established
- Alternatives did not have all the answers
- VOC limits on solvents were changing as were test methods
Many manufacturers are turning to "no-clean" processes implying that cleaning is not required after soldering. In the "no-clean" process, rosin and activator are not removed prior to the next process such as coating or encapsulating of the PCB. Such residues, along with any other unwanted elements collected due to the missing cleaning stage, could cause issues with adhesion and possibly affect the performance of the protecting media applied. It can therefore be stated that even with advances in new technologies, such as "no-clean" fluxes, cleaning is still an essential multi-stage process within the electronics industry. Finally, there are also cleaning stages required for the removal of coatings and adhesives when re-work is necessary and for the cleaning of actual components and for maintenance of the production line.
If there's a product or topic you'd like to see The Q Source Resource write about please let us know. We'd also appreciate if you share this blog post with your friends and colleagues via the social media links below. If you have questions or comments about ACL Staticide products or about cleaning printed circuit boards and electronic equipment please leave us a message in the comments section.
For additional Q Source product information, reviews, how-to articles, and special offers please subscribe to our email newsletter.
Labels:
ACL Staticide,
aerosol cleaners,
EPA,
Guest Blog,
smog,
Steve Allen,
VOC,
volatile organic compound
Thursday, April 24, 2014
3M Receives EPA ENERGY STAR Sustained Excellence Award for Record 10th Year in a Row
In an Earth Day announcement, 3M revealed yesterday that they have earned a privilege that no other industrial company in the world has attained. For the 10th year in a row, the United States Environmental Protection Agency (EPA) has presented 3M with the EPA ENERGY STAR® Sustained Excellence Award.
Recognizing the importance of energy efficiency and environmental concerns as a strategy for corporate social responsibility, 3M stated that they've worked the past 10 years (and longer) to improve their processes, raw materials, and efficient methods for resource savings. Among 3M's sustainable products are 3M Novec Engineered Fluids, 3M Window Films, and 3M LED Advanced Lighting.
The EPA recognized 3M for a number of efforts including:
In related news, 3M received the Xcel Energy 2013 Energy Efficiency Expo Award for saving nearly 1.8 million therms of gas. And in an effort to further solidify their commitment to corporate responsibility, 3M became a member of the United Nations Global Compact, a voluntary initiative that outlines 10 doctrines in the areas of human rights, labor, environment, and anti-corruption.
Q Source has been an authorized distributor of 3M products for more than a decade. We congratulate them on their recognition and continued sustainability efforts.
For additional Q Source product information, reviews, how-to articles, and special offers please subscribe to our email newsletter.
Recognizing the importance of energy efficiency and environmental concerns as a strategy for corporate social responsibility, 3M stated that they've worked the past 10 years (and longer) to improve their processes, raw materials, and efficient methods for resource savings. Among 3M's sustainable products are 3M Novec Engineered Fluids, 3M Window Films, and 3M LED Advanced Lighting.
The EPA recognized 3M for a number of efforts including:
- Implementation of 252 projects, which resulted in savings of $8.79 million and 61,700 metric tons of CO2
- Development of a strategic initiative to identify and implement projects to make step-change improvements in greenhouse gas emissions and energy efficiency
- Formation of Centers of Excellence to integrate all aspects of sustainability into business strategies company-wide
- Enacting energy-saving innovations in diverse markets, and engaging communities globally in energy and sustainability dialogues

In related news, 3M received the Xcel Energy 2013 Energy Efficiency Expo Award for saving nearly 1.8 million therms of gas. And in an effort to further solidify their commitment to corporate responsibility, 3M became a member of the United Nations Global Compact, a voluntary initiative that outlines 10 doctrines in the areas of human rights, labor, environment, and anti-corruption.
Q Source has been an authorized distributor of 3M products for more than a decade. We congratulate them on their recognition and continued sustainability efforts.
For additional Q Source product information, reviews, how-to articles, and special offers please subscribe to our email newsletter.
Tuesday, April 22, 2014
Brady BMP41 Label Printer on Flickr
The Brady BMP41 Label Printer is a durable, portable printer for all your industrial labeling needs. The BMP41 features built-in templates, smart-cell technology, and the ability to print both continuous and die-cut labels. Check out this Flickr photo set to get a closer look at this durable and versatile portable printer.
Be sure to visit our Web site to learn more about the Brady BMP41 Label Printer.
Be sure to visit our Web site to learn more about the Brady BMP41 Label Printer.
Labels:
Brady BMP41 Label Printer,
continuous labels,
die-cut labels,
Flickr,
industrial printing,
smart-cell technology
Wednesday, April 9, 2014
Why Clean "No Cleans?" Printed Circuit Board Flux Removal – Guest Blog
by Steve Allen, VP Marketing and Innovation, ACL Staticide
Steve Allen, our guest blogger from ACL, returns with this article about cleaning “no-clean” fluxes.
Today, nearly half of all printed circuit boards (PCBs) are assembled with no-clean solder paste. The development of no-clean solder paste was initiated to eliminate the need for further post-solder cleaning of circuit boards. Yet, many electronics assemblers are still struggling with the process of adequately and effectively removing no-clean flux materials.
No-clean fluxes are now the most popular fluxes to clean in electronics manufacturing. Most manufacturers have designed and dialed in their assembly lines to run no-clean paste. And, they only clean the boards they want to clean, not always the boards they perhaps need to clean. Additionally, the flux residues left behind by no-clean pastes are more difficult to remove from PCBs than other fluxes. Since they are formulated not to be cleaned, the residues from no-clean products can be left on the board in unwanted areas with detrimental effects on the PCB. That creates a cleaning challenge if you need to clean off a residue that was not designed to be removed.
No-clean flux and solder residue on the board depends on the amount of solids in the material, the type of gelling agents, and various activators in the flux. The fluxes in most of today's no-clean pastes contain up to 60% solids. The lower the total solids, the fewer residues on the board. No cleans, in theory, contain lower total solids so as not to need removal/cleaning. Following the reflow process, the flux leaves a small amount of residue around the various solder joints.
There are several reasons to remove no-clean flux residues from PCBs. Historically, no-clean fluxes were developed as tacky resins, which inherently coated and stuck to all surfaces. The residue would gradually build up on the test pins. Manufacturers began cleaning no-clean fluxes when problems emerged with in-circuit testing. The latest technologies of no cleans are improved and no longer tacky, but still can interfere with signal transmission in most instances.
Also, no-clean fluxes can inhibit proper adhesion of conformal coatings. No-clean flux residues can absorb moisture in process. In any further curing processes, the release of any moisture can cause the coating to be separated from the board and incomplete conformal adhesion can occur. This can allow corrosive materials, carbon dust build-up, or moisture to penetrate under the assembly and cause corrosion, signal transmission problems, and component failure.
Today, no-clean paste manufacturers are aware that end-users are cleaning no cleans from board surfaces. The type of flux chemistry chosen can have significant impact on the cleaning process. To effectively clean and remove no-clean solder pastes and no-clean flux residues, a polar solvent or a solution of water and saponifier is necessary. Most no-clean pastes require an organic saponifier for effective flux removal, but some can be cleaned with inorganic saponifiers. No-clean fluxes that contain halides leave the most residue and are easier to clean. However, halide-free no-clean fluxes produce less residue, yet are more difficult to remove. In general, no-clean fluxes can be extremely difficult to clean, particularly following any reflow processes, as they can be baked on and tough to remove.
It can be vitally important to resolve any issues with no-clean technologies and their subsequent cleaning challenges at the forefront of the device design process especially with high-reliability products such as avionics or medical devices. In applications where cleanliness is critical, it is important to consult cleaning experts like ACL for the most effective, board-safe cleaning technology.
Q Source would like to, once again, thank our guest blogger, Steve Allen. We appreciate your contributions to The Q Source Resource and look forward to sharing your future articles, as well.
For more information about ACL Staticide products and options for flux removal, please visit the ACL Staticide Department at QSource.com.
For additional Q Source product information, reviews, how-to articles, and special offers please subscribe to our email newsletter.
Steve Allen, our guest blogger from ACL, returns with this article about cleaning “no-clean” fluxes.
Today, nearly half of all printed circuit boards (PCBs) are assembled with no-clean solder paste. The development of no-clean solder paste was initiated to eliminate the need for further post-solder cleaning of circuit boards. Yet, many electronics assemblers are still struggling with the process of adequately and effectively removing no-clean flux materials.
No-clean fluxes are now the most popular fluxes to clean in electronics manufacturing. Most manufacturers have designed and dialed in their assembly lines to run no-clean paste. And, they only clean the boards they want to clean, not always the boards they perhaps need to clean. Additionally, the flux residues left behind by no-clean pastes are more difficult to remove from PCBs than other fluxes. Since they are formulated not to be cleaned, the residues from no-clean products can be left on the board in unwanted areas with detrimental effects on the PCB. That creates a cleaning challenge if you need to clean off a residue that was not designed to be removed.
No-clean flux and solder residue on the board depends on the amount of solids in the material, the type of gelling agents, and various activators in the flux. The fluxes in most of today's no-clean pastes contain up to 60% solids. The lower the total solids, the fewer residues on the board. No cleans, in theory, contain lower total solids so as not to need removal/cleaning. Following the reflow process, the flux leaves a small amount of residue around the various solder joints.
There are several reasons to remove no-clean flux residues from PCBs. Historically, no-clean fluxes were developed as tacky resins, which inherently coated and stuck to all surfaces. The residue would gradually build up on the test pins. Manufacturers began cleaning no-clean fluxes when problems emerged with in-circuit testing. The latest technologies of no cleans are improved and no longer tacky, but still can interfere with signal transmission in most instances.
Also, no-clean fluxes can inhibit proper adhesion of conformal coatings. No-clean flux residues can absorb moisture in process. In any further curing processes, the release of any moisture can cause the coating to be separated from the board and incomplete conformal adhesion can occur. This can allow corrosive materials, carbon dust build-up, or moisture to penetrate under the assembly and cause corrosion, signal transmission problems, and component failure.
Today, no-clean paste manufacturers are aware that end-users are cleaning no cleans from board surfaces. The type of flux chemistry chosen can have significant impact on the cleaning process. To effectively clean and remove no-clean solder pastes and no-clean flux residues, a polar solvent or a solution of water and saponifier is necessary. Most no-clean pastes require an organic saponifier for effective flux removal, but some can be cleaned with inorganic saponifiers. No-clean fluxes that contain halides leave the most residue and are easier to clean. However, halide-free no-clean fluxes produce less residue, yet are more difficult to remove. In general, no-clean fluxes can be extremely difficult to clean, particularly following any reflow processes, as they can be baked on and tough to remove.

Q Source would like to, once again, thank our guest blogger, Steve Allen. We appreciate your contributions to The Q Source Resource and look forward to sharing your future articles, as well.
For more information about ACL Staticide products and options for flux removal, please visit the ACL Staticide Department at QSource.com.
For additional Q Source product information, reviews, how-to articles, and special offers please subscribe to our email newsletter.
Labels:
ACL Staticide,
flux remover,
Guest Blog,
no-clean flux,
PCB cleaning,
printed circuit boards,
Steve Allen
Thursday, March 13, 2014
Q&A: A Look at Hog Heaven Mats w/Mike Andersen of The Andersen Company
Q Source: Hi Mike. We're excited to have the Andersen Company line on QSource.com. Can you tell our readers a little about your company?
Mike Andersen: Hi. Sure. The Andersen Company has a 40-year history of bringing innovative products to the market that solve problems and provide years of service. We have more than 70 products and a number of popular lines such as Waterhog, Comfort Flow, Cushion Max, Happy Feet, and the line we're looking at today, Hog Heaven.
Q Source: Okay, great. Please tell us about your line of Hog Heaven Mats.
Mike Andersen: American made Hog Heaven anti-fatigue mats, like all of our products, were created to address a particular issue. Studies have shown that standing on a hard surface for hours at a time lowers worker productivity and comfort. Hog Heaven mats solve this problem.
Q Source: How do Hog Heaven mats address this problem? What makes them different from other mats?
Mike Andersen: These mats are made with a 100% nitrile rubber top and a closed-cell nitrile/PVC-blended cushion, which sets them apart from other anti-fatigue mats. Nitrile rubber is grease- and oil-proof and will not crack, curl, or break like other PVC products often do. In addition, the foam cushion is molded, not glued, to the rubber top, which eliminates the possibility of delamination.

Q Source: Are they available in different styles?
Mike Andersen: They're available with beveled borders that provide safe transitions. Yellow-, red-, orange-, and green-striped borders are also available, as well as the black borders.
Q Source: What available sizes do you offer?
Mike Andersen: Hog Heaven is available in two thicknesses: 5/8" and 7/8". So you can choose your thickness depending on the level of comfort desired. Sizes include 33", 46", and 58" widths, and lengths up to 60' in one-foot increments.
Q Source: Thanks for the helpful information about Andersen's Hog Heaven mats. We're sure it will help our customers make an informed purchase when selecting the mats they need. Is there anything else you'd like to say about Hog Heaven?
Mike Andersen: Yes, thank you. If you need a benefit-loaded anti-fatigue mat that will last for years, Hog Heaven is the right choice for you.
To place an order for Andersen Hog Heaven Mats (,M+A Matting) or other Andersen Company.
For additional Q Source product information, reviews, how-to articles, and special offers please subscribe to our email newsletter.
Labels:
anti-fatigue mats,
Comfort Flow,
Cushion Max,
Happy Feet,
Hog Heaven,
Mike Andersen,
Q&A,
The Andersen Company,
Waterhog
Subscribe to:
Posts (Atom)